
Project Description
Recently there has been growing interesting in the field of soft robotics, which features robots that are flexible yet robust. A Tensegrity robot is a form of soft robot that is comprised of a series of rods under compressional load joined together by cables under tensional load; through proper actuation of those cable it can move across undulating surfaces. The BEST lab at UC Berkeley has collaborated with researchers from NASA Ames Research Center to explore the use of tensegrity robots for a variety of purposes. In this project, seven MEng students split into two groups to build two prototypes: the sphere tensegrity robot and the spine tensegrity robot.
Spherical Tensegrity
The project team of Peadar Keagan, Li Xiang, Azharuddin Khaderi and Alex Lim designed, manufactured, and simulated a new and improved Spherical Tensegrity robot prototype. This new prototype actuates cables using motors in the center of each rod and has captured the interest of NASA, who may use these robots for planetary exploration as the robots reduce the complexity of landing on another planet and can traverse through a wide range of terrains.
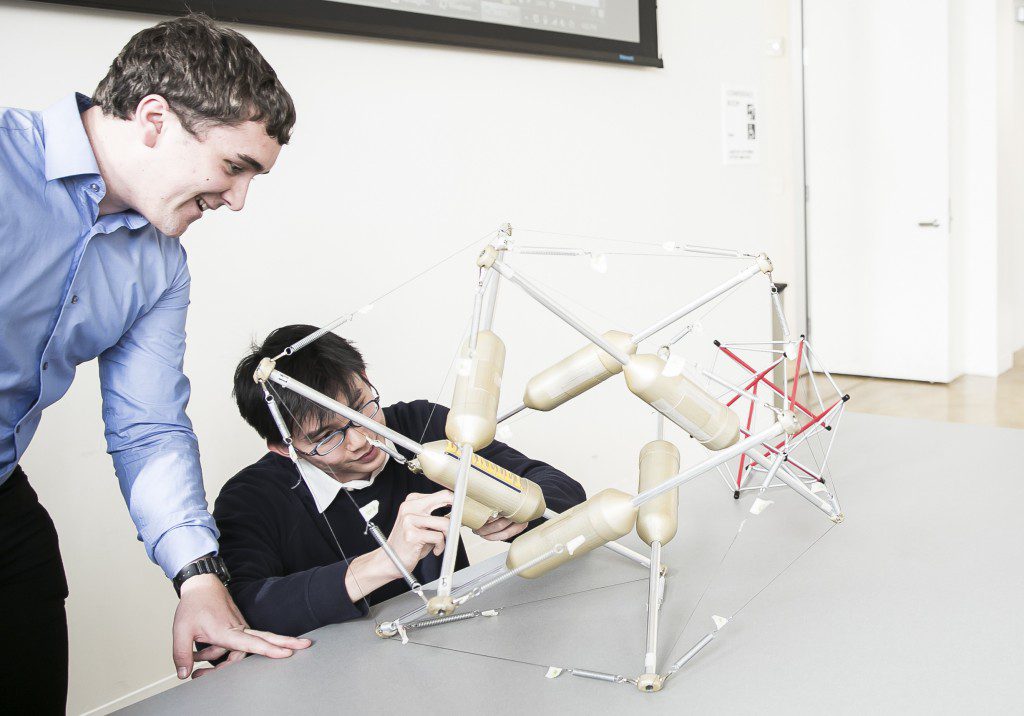

Spine Tensegrity
The project team of ChanWoo Yang, Patrick Hylton, and Yakshu Madaan simulated, designed, and manufactured a new Spine Tensegrity robot prototype called the ULTRA Spine. The Spine robot replicates the motion of a vertebrate’s spine and explores new horizons concerning how robotic motion will be influenced by a flexible core.
Sphere
In existing technologies, the rover and the lander are two separate vehicles and the lander itself is comprised of various subsystems, causing the landing procedure to be costly and complicated. With the introduction of the spherical tensegrity robot, the rover and the lander integrate into one vehicle. This is due to the intrinsic shock absorbency of a tensegrity structure. Additionally, this feature lessens the amount of damage that may occur to the rover; if any parts of the robot gets damaged or breaks, the robot’s other parts can pick up the slack. Ken Caluwaerts, a roboticist at Ghent University in Belgium, embraces this idea, as he is developing a distributed system of control so that if a quarter of the motors fail, the structure should be able to continue rolling.
Due to the nature of the tensegrity rover’s design, it can be compacted into a small area for travel, allowing a single spacecraft to carry a number of these rovers for multiple deployments and increasing the efficiency of NASA’s information gathering from multiple sites in one mission.

Spine
Technology has dramatically advanced in the last couple of decades, yet few robots today are capable of mimicking the complex dynamics of a biological creature, specifically that of quadruped and humanoid robots. In fact, most fail in attempting to combine compliance, being lightweight, flexibility, underactuation, and modularity. The issue is, rigid body platforms in robots not only restrict robotic motions, but also decrease the overall durability of hardware structures, which consequently leads to heavier and thicker robotics hardware design.
Therefore, the Underactuated Lightweight Tensegrity Robotic Assistive Spine (ULTRA Spine) team at UC Berkeley is developing a spinal robot based on tensegrity structures that can make essential spinal motions: bending in x and y axes, and torsional about the z axis. Ultimately, we are anticipating that robots with this ideal robotics body platform will allow more freedom to generate complex motions, and it will increase the practicality and broaden the application of quadruped/biped robots in the future.

Accomplishments
The sphere team built a new and improved Spherical Robot prototype that is lighter, faster, more energy efficient, and sleeker than the previous prototype. The team will write journal and conference papers based on the design process, electronics, simulation and controls of the new prototype, and then apply for a patent.
The very first tensegrity spine robot’s simulations and mechanism design works were submitted and accepted to ASME 2015 International Design Engineering Technical Conference. The team will complete the manufacturing and assembly of the robot, and will continue to work on the dynamics of tensegrity spine robotics modeling and control system designs.

Faculty Advisor
Professor Alice Agogino
The MEng team provided valuable multidisciplinary innovations for this cutting edge NASA project that involved mechanical and electrical design, software simulations and controls. The Intelligent Systems Division at NASA Ames is learning from their final prototype to modify their production system.
← View all Capstone Projects